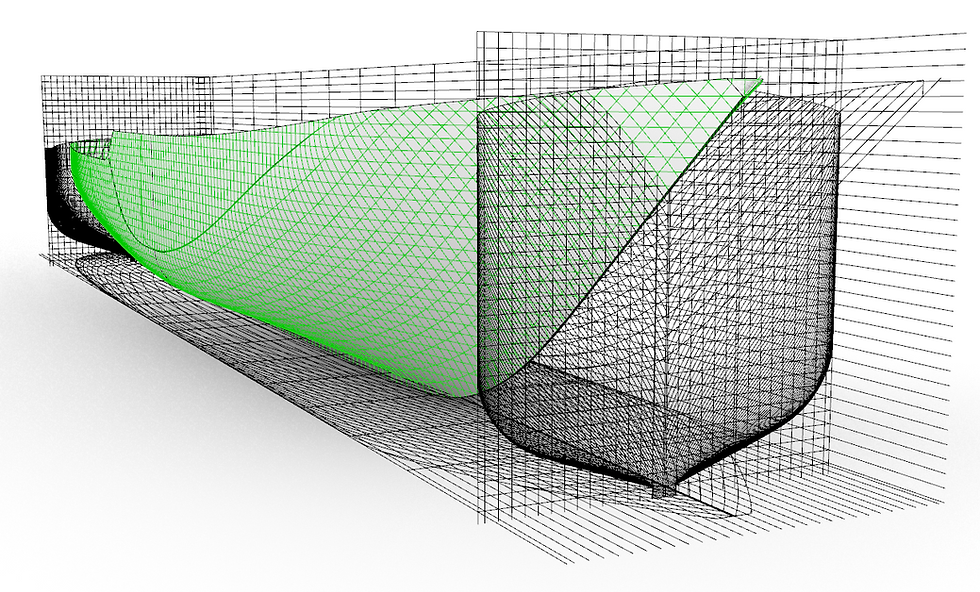
Here I will try to answer the most frequently asked questions about Shape Maker.
1. Where to start?
The easiest thing to do is download and install SM. You can download the program here. Installation takes a few minutes and after that the SM is ready to go. As in any other business, mastering everything new requires some effort. Before getting started, I would recommend reading the SM training guide. The first chapters describe the basic principles of work and the commands. After that, I recommend that you pay special attention to the chapter "First Project", which shows step by step the construction of the surface of the ship's hull. I recommend that you go through the entire process of modeling a surface as described in this chapter. As a result, you will gain basic skills in working with the program and will have the first completed ship hull model. The video section also has a lot of information on how to work with SM. Questions about SM can also be asked on the forum. To do this, you need to register on the site as a member.
2. What do you need to know to work with SM?
The first thing you need to work with SM is the knowledge of the basic principles of definition a ship's surface. No, even the most advanced program can replace your personal idea of the shape of the ship's surface. Of course, it is also necessary to have an understanding of the curves and surfaces used in SM. Some information can be found here on the website. Everything else can be learned as you study SM.
3. How is SM different from other programs?
There are a lot of programs that use NURBS curves and surfaces for modeling. All of them differ in the way surfaces are formed and the organization of the program itself. I would highlight the three most important differences:
- the ability to use the program at any stage of the project, with a gradual refinement of the shape of the hull at subsequent stages of the project. That is, the surface is not created each time anew, but is modified from the very initial stages of the project to the stage of detailed design and construction.
- a wide range of surface quality control tools and the possibility of local shape correction allows you to implement any designer's ideas and bring them to the detailed design stage.
- the presence of topology in the surface model makes it possible to easily change the shape of both boundary curves and surfaces and at the same time avoid the occurrence of cracks and gaps between surface areas.
4. Can I use SM in the early stages of a project, or is this program only for final surface smoothing?
Surface modeling at the initial stages of the project can and should be done in SM. As initial data, you can use the drawings of the general arrangement - profile, deck plans and midship - frame. The topological surface model makes it easy to create and transform models at the initial stages of a project. You can also use the models of previous projects. Scale them to new dimensions, combine fore and aft ends from different hulls and thereby quickly create a new hull surface. for preliminary calculations. As a rule, such cases look well-designed and make a good impression on a potential customer. The presence of a good library of ship hulls in the company can significantly save time on creating new models.
5. Will there be gaps between the surfaces if I change the shape of the common boundary line?
The surface model in SM has a boundary representation. That is, the surface patches are based on boundary curves and corner points. A change in the position of a corner point leads to a change in the boundary curves and, accordingly, surfaces coming into it. Changing the shape of the boundary curve will change the shape of the surfaces resting on it. Two patches of the surface having a common boundary curve will under no circumstances have gaps along this boundary. You can read more about this here.
6. The shape of the surface changes too much when moving a single control point with the mouse. What to do?
NURBS surfaces that are used in SM are also called sculpted surfaces. The required shape of the surface is achieved by changing the position of the points of the control polyhedron. In the case of working with the surface of the ship's hull, even moving the cursor by one pixel of the screen will lead to a shift of tens and millimeters on the real scale of the ship. When moving the mouse, we can control the minimum offset by 5-10 pixels. It's too rough to smooth the surface, especially if we're working with curvature and inflection lines. To do this, SM has the ability to scale the movement of the cursor. When using this option, you can move the points of the control polyhedron by a millimeter or even tenths of a millimeter at the ship's scale.
7. There are too many control points on my surface. Why is this happening?
The number of points in the control polyhedron depends on the number of points on opposite boundary lines. The same number of points on the boundaries will give the same number of points on the surface. An arbitrary number of points on the boundary curves can give a very large number of points in the surface control polyhedron. In this case, the points of the polyhedron are likely to be unevenly distributed over the surface. It will be difficult to work with such a surface. I recommend using "magic" numbers when assigning the number of curve control points. You can find out more about this here.
8. How to change only one line projection and leave the other one unchanged?
All lines in SM are spatial lines. In order to keep the shape of the line on one of the projections when modifying the control points, use the ORTO cursor mode when modifying the curve. In this case, the saved projection of the curve will not change.
9. Why does trimming of surfaces and lines disappear?
Lines and surfaces in SM are not physically trimmed. Instead, it is possible to hide part of a line or surface when rendering. To do this, in the visualization levels there is a special level of turning on and off the visualization of trimming lines and surfaces.
10. Can I load and edit surfaces from other programs?
Loading surfaces from other programs is possible in SM by importing IGES files. It is possible to edit such surfaces, but the loaded surfaces will not be topologically connected to each other, and if the boundary of the surface is changed, the surface adjacent to this boundary will not be updated. A gap will appear between the surface areas. You can add a topology manually. The most reasonable approach is to use such surfaces only as prototype surfaces. Each of the surface design systems has its own characteristics and problems. It would be foolish to copy them into a new model. As an example, I can give a NAPA surface consisting of 200-300 surface patches. Editing such a surface in SM is very laborious. A smoothed surface based on such a prototype in SM will contain only 10–12 surface patches.
11. Why can't I achieve the desired surface shape?
There can be many reasons for this. The key to successful surface modeling can be correct subdivision of the surface. I already talked about it here. Proper partitioning into surface patches can significantly reduce the modeling time. Here you can learn more about.
12. The control points of the surface are uneven, but the shape of the sections suits me. Is it so important to have a nice grid of surface control points?
I believe that the control polygon mesh should be uniform and smooth. If possible, repeat imaginary streamlines around the surface. Grid cells should be as rectangular as possible. This greatly simplifies surface smoothing. It is best to try to do this in the earliest stages of surface formation. In this case, the law of distribution of control points will be preserved with their subsequent increase. A beautiful mesh is the key to a beautiful surface. A well-defined mesh also simplifies the process of reshaping a surface. Copying a poorly defined surface mesh into a new project will cause more problems in subsequent new projects.
13. How can I change the surface, but keep the previous result?
SM has a fairly simple but effective surface revision system. It is enough to make a copy of the project block. This is very handy if you want to keep a history of the major revisions of a project. For example, changes made to the body surface for a new CFD run. You can change the color of the surfaces of the previous revision. This will make it easier to compare the two cases. This approach will allow you to control the introduction of changes at the final stage of the project, when you need to control the area of surface change. More information here.
14. How to quickly calculate the characteristics of the underwater volume?
For the correct calculation of the underwater volume, the surface of the hull must be closed, without holes and slots. As a rule, at the initial stages of the project, the upper deck, which closes the hull volume, is not modeled. Instead, you can set the level below which the hull should be closed.
15. What information from SM can I use in other programs?
SM produces several different types of documentation in DXF format in 2D and in 3D which can be used both for making drawings and check builds, as well as for producing shell plates unfoldings and cutting them. Surface in IGES format can be transferred to work in almost any of the 3D modeling programs. The surface is transferred with absolute mathematical precision.
16. How can I use an existing model in a new project?
Often, in the process of designing a new vessel, the surface of a previous project, a close prototype, is used in the initial stages. In this case, the blocks of the hull surface can be copied into a new project and transformed according to the new dimensions of the vessel. After that, the model can be modified to the specific requirements of the new project. You can also combine fore and aft ships from different projects. You can find out more about this here.
17. The surface of the hull is ready and put into production. How local can changes in such a surface be?
As a rule, after launching into production, the surface of the case does not change, but sometimes it becomes necessary to change the surface locally. When doing this, it is very important to make sure that the area of changes does not affect those areas of the surface that are already under construction. To do this, a new revision of the hull is made, the required changes are made and, after that, the new surface is compared with the previous one. For local changes, you may need to increase the control points of the surface. Increasing control points does not change the surface.
18. Can I model the surfaces of superstructures and protrusions in SM?
In SM, you can model both superstructures and any appendages, as well as internal curved surfaces. For example, the lining surfaces of ship’s holds.
19. My model is too big. How can I structure it?
To do this, you can use a more detailed partition of the block tree. Its structure does not have any restrictions. Blocks can be turned on, off, locked for editing, as well as control the visualization of elements of different colors and types inside the block. The user can also set an arbitrary block as an entry point and only this branch of the tree will be rendered.
20. How to understand that the surface is smooth enough?
Mathematical criteria for the smoothness and smoothness of curves and surfaces are not always applicable in shipbuilding. I will give a simple example - sine and cosine are infinitely smooth functions with the continuity of all derivatives, but no one is use them when modeling the surface of a hull. Another example - the line of the vertical side and the flat bottom, when passing into the radius of the bilge, have continuity only along the tangent, but not along the curvature. There are several ways to check the smoothness of curves and surfaces in SM: curvature plots, kink lines, and lines of equal slope to the surface. All this helps in controlling the shape of the surface, but we should not forget about the technological aspects of the surface. No one will bend a surface with bending radii less than the permissible ones, or bend it poorly. You can see more about this here.
21. Why can't I build the surface of the entire hull in one piece of surface?
SM has no limit on the number of surface areas. To build a surface model, such as a classic yacht, you can use one area of the surface. If your boat's hull has a flat side, a flat bottom, and break lines, then it makes more sense to break it up into several sections. In this case, it is much easier to control the shape of the surface. You can learn more about this here.
Commentaires