Ship’s hull in a good shape.
- Alexander Alexanov
- Feb 25, 2021
- 2 min read
Updated: Feb 26, 2021

Friend of mine found nice and simple program for hull lines fairing. He said he spent just few minutes and hull lines was ready. Only one remark - he is not ship designer or shipbuilder, he is IT specialist. I had spent some evenings surfing in Internet and found a lot of videos with examples of hull lines fairing in different programs. Some of this programs especially design for hull surface modeling, some of them even universal mechanical CADs. So lines fairing is so simple that everyone can do it in any CAD software with NURBS surfaces tools, but in reality it is not true.
Workshop documentation for hull building process is quite time consuming process. Only special ship design software used for that. Depending from ship’s size several engineers work several months on such project. At same time hull surface fairing is job for one person for one or two weeks. Cost of lines fairing in total cost of workshop documentation is about 1-2% but problems with hull lines will compromise all workshop documentation. Hull surface is like basement for all hull structures. I don’t think you will build a house if something wrong with basement, but I have a lot of examples of workshop documentation based on wrong surface.
Why it may happened:
Lines fairing software not intended to use for production lines fairing,
Not fully understanding that Nurbs nature is not same as spline,
Poor tools for surface quality checking,
Luck of experience in lines fairing (to do it correctly you have to practice every time).
What's may be wrong when using bad shaped hull surface:
Wrong shape of bended shell plates,
Shell plates and connected to shell profiles have a different curvature and needs extra welding to fill gaps,
Gaps between inner plate parts and shell, need to have extra welding,
Deformation of the shell plates from extra welding and hitting,
Deformation whole unit due to extra hitting and internal stress in constructions.
All this factors increase production time, require more welding, reduce building quality, create more stressed constructions and, as result, create cracks and internal defects during hull life time.
Possible losses:
Remodeling and update workshop documentation if problem detected at modeling stage,
Nesting new parts or fix if problem was detected at steel cutting stage,
Rebuilding stricture if problem arise at unit building stage.
Hull lines is a small part of workshop documentation, but can create a big problem. In most of hull surfaces models, I have had for fairing or just for check, I saw at least some areas which can be improved. I am strongly recommended to check your surface twice before start workshop documentation. If you need some expert opinion – you can send it to me. It is always good to look at something with fresh eye before start big and expensive project.
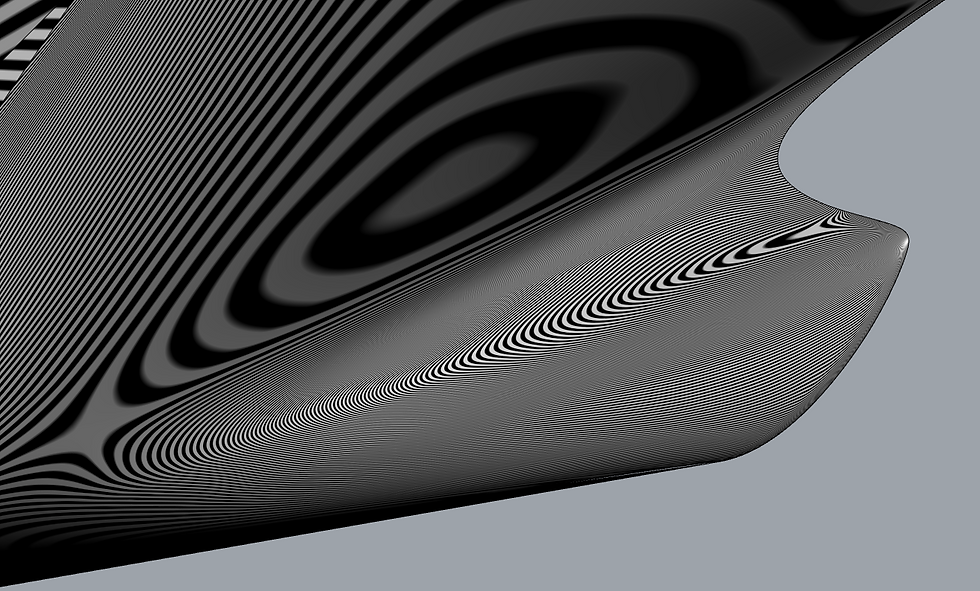
Comments